1.2 Дефектування й контроль типових деталей
Найбільшу частку в деталях становлять циліндричні поверхні (зовнішні та внутрішні) — поверхні під підшипники, втулки, манжети тощо.
Рисунок 1.2.1 Типова будова кулькового підшипника кочення: 1 - зовнішнє кільце; 2 - тіло кочення; 3 - сепаратор; 4 - канавка; 5 - внутрішнє кільце.
Рисунок 1.2.3 Ущільнювальні манжети
Рисунок 1.2.4 Будова мікрометру: 1 - скоба ; 2 - п´ятка ; 3 - мікрометричний гвинт ; 4 - стопорний пристрій; 5 - стебло ; 6 - барабан ; 7 – корпус тріскачки.
Вимірювання мікрометром
Рисунок 1.2.5 Нутроміри: а) нутромір індикаторного типу; б) мікрометричний нутромір три-точковий з діапазоном вимірювань 17...20 мм; в) набір кінцевих мір для калібрування нутроміра
Індикаторні засоби вимірювань
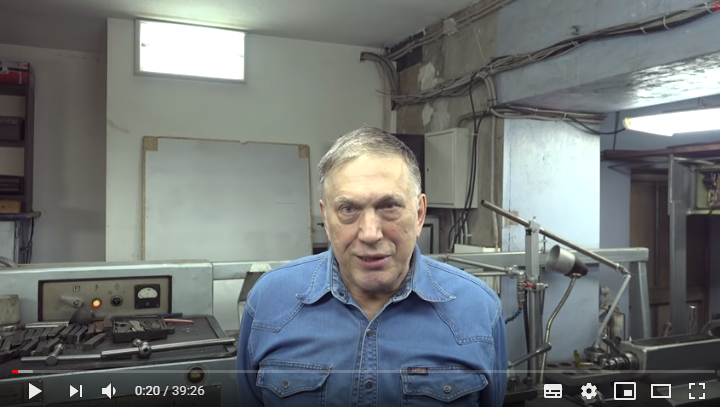
Діаметри отворів під підшипники та гнізда підшипників у корпусах
обробляють за сьомим квалітетом (поле допуску — 0,030–0,045 мм). Їх спрацювання
допускається до 0,020–0,030 мм. Відхилення форми регламентують для поверхонь,
які утворюють із підшипниками кочення посадки з натягом. Воно не повинно перевищувати половини поля допуску на розмір поверхні.
Для інших у межах поля допуску. В окремих випадках доводиться вимірювати
отвори, які утворені двома деталями (роз’ємні отвори), зокрема опори корінних підшипників колінчастих валів.
Схема та принцип роботи кривошипно-шатунного
механізму. Колінчастий вал зображено червоним кольором.
У таких випадках слід ретельно дотримуватися вимог документації.
Наприклад, у блок-картерах холодильних компресорів та їх модифікацій кришки корінних опор мають бути затягнуті моментом 260–280 Н‧м, а бічний гвинт, який притискає кришку до блока в
горизонтальному напрямку, має затягуватися моментом 16–18
Н‧м.
Рисунок 1.2.6 Компресор промислової холодильної установки
Рисунок 1.2.6 Компресор промислової холодильної установки
Поняття про посадки
Рисунок 1.2.7 Калібри для контролю зовнішньої різі (вгорі) і
двосторонній для контролю внутрішньої різі (внизу)
Різьба має бути повною, чистою, без задирок, ум’ятин, забитості,
викришених і зірваних ниток. Болти, шпильки, гайки та пробки, які мають більш як дві зірвані нитки різі, бракують. Нарізні
отвори в деталях і різі валів треба ремонтувати.
Не допускається використання болтів, пробок і гайок із зім’ятими
гранями. У разі спрацювання граней понад 0,5 мм (від розміру за кресленням) вказані деталі вибраковують.
Стрижні болтів і шпильок не можуть мати згин і помітне спрацювання. Під
час розбирання справні шпильки з деталей не слід вивертати, за винятком окремих
обумовлених випадків.
Стан поверхонь зубів шестерень визначають спершу з допомогою оглядання. В разі злому зубів та їх
викришування використання шестерень не допускається. Якщо немає бракувальних
ознак, оцінку придатності шестерень визначають на основі вимірювання зубів одним
із трьох способів, визначених заводом-виробником — вимірюванням довжини спільної
нормалі кількох зубів штангенциркулем або нормалеміром (мікрометричним чи індикаторним); вимірюванням товщини окремого зуба
(також і в ланцюгових зірочках) штангензубоміром і вимірюванням штангенциркулем за двома діаметрально розміщеними
стандартними роликами, вкладеними між двох шліців або зубів.
Рисунок 1.2.8 Штангенінструмент для дефектування зубів шестерень:
а) штангенциркуль; б) штангензубомір
Останнім способом також оцінюють придатність евольвентних шліців. Діаметри стандартних роликів (3,47–9 мм) і відстань за роликами
наведено в технічних вимогах на дефектування відповідної машини. Дефектування
прямобічних шліців виконують, зазвичай, штангенциркулем або шаблоном. Спрацювання шліців допускається в межах 0,4–0,8
мм.
Вимірювання довжини спільної нормалі проводять після попереднього налаштування інструмента на нормальне чи допустиме значення й подальше доведення вимірювальних губок інструмента до контакту з крайніми зубами. Кількість зубів, що при цьому охоплюються, не обумовлюється.
Рисунок 1.2.9 Види зубчастих передач:
В залежності від розташування зачеплення, зубчасті передачі поділяться
на: а) зубчасті передачі з зовнішнім зачепленням; б) зубчасті передачі з внутрішнім зачепленням.
В залежності від положення осі зуба відносно осі валу, зубчасті передачі поділяться на: а, б, д) прямозубі; в, е, з) косозубі; г) шевронні; ж) кругові.
Рисунок 1.2.10 Види зачеплення зубів зубчастих
передач.
В залежності від профілю зубів, зубчасті передачі поділяться на:
а) зубчасті передачі з евольвентним профілем зубів; б) зубчасті передачі з циклоїдальним профілем зубів; в) зубчасті передачі з профілем зубів, виконаним по дугах кіл
(зачеплення Новикова).
Придатність радіальних підшипників кочення оцінюють за результатами зовнішнього огляду, перевірки плавності вибігу (дає змогу виявити невидимі дефекти доріжок і тіл кочення чи сторонні частинки) і вимірювання радіального зазору.
Надійність підшипників. Зазори в підшипнику
Під час огляду визначають цілісність деталей, стан бігових доріжок, кульок і роликів, сепараторів. Спрацювання підшипників (радіальний зазор) визначають на спеціальних пристосуваннях різних конструкцій, в яких підшипник закріплюють за внутрішнім кільцем, а до зовнішнього підводять індикатор годинникового типу.
Вимірювання радіального зазору підшипників
Рисунок 1.2.11 – Прилад перевірки зазорів КИ-1223: 1 - плита; 2 - траверса; 3 - конус; 4 - гвинт; 5 - каретка; 6 - напрямна; 7 - індикатор; 8, 9 - гвинт; 10 - підшипник
Рисунок 1.2.12 Будова індикатора годинникового типу: 1 - ручка для підйому і опускання вимірювального стрижня; 2 - кільце встановлення початку відліку; 3 - мала стрілка [мм]; 4 - уставні вказівки допуску; 5 - велика стрілка; 6 - кругова шкала індикатора; 7 - втулка вимірювального стрижня; 8 - вимірювальний стрижень; 9 - вимірювальний наконечник; 10 - відлікова (мала) шкала [мм].
Переміщуючи рукою зовнішнє кільце в напрямку переміщення стрижня
індикатора, визначають радіальний зазор. Операцію повторюють у кількох
місцях.
Допустиме значення радіального зазору
підшипників кочення тим менше, чим відповідальніше місце його встановлення.
Для дефектування підшипників не обов’язково демонтувати їх із валів. Оскільки підшипники кочення завжди напресовують на вали, а безпідставний демонтаж їх із валів погіршує і вал, і підшипник, тож якщо немає послаблення
посадки та інших дефектів на валу і в підшипнику, радіальний зазор підшипника
можна виміряти з допомогою стойки з індикатором на токарному верстаті, закріпивши вал із підшипником у патроні.
Придатність конічних підшипників кочення оцінюють так само, за винятком спрацювання. Для конічних підшипників
визначається монтажна висота, яка являє собою відстань між протилежними торцями
внутрішнього і зовнішнього кільця.
Виміряти монтажну висоту можна різними способами: на перевірній плиті, використовуючи штангенрейсмас або штангенциркуль ШЦ-0,1-125 із висувним глибиноміром, або будь-яким штангенциркулем, утримуючи підшипник у руках. У цілому, в конусних підшипниках не допускають виступу роликів над зовнішнім кільцем.
Рисунок 1.2.13 а) штангенрейсмас тип ШР ГОСТ 164-90; б) штангенциркуль ШЦ-0,1-125
Під час дефектування пружин з допомогою оглядання визначають цілісність витків, відсутність тріщин,
забоїн, корозії, згину, нерівномірність кроку витків (якщо згин і нерівномірність кроку очевидні), вимірюють згин,
нерівномірність кроку витків, не перпендикулярність торців до осі, зусилля, яке пружина створює під час стискання (розтягування — для пружин розтягування) до робочої висоти (довжини), тобто тієї висоти (довжини), за якої
пружина перебуває в робочому стані.
За наявності на поверхні пружини тріщин, забоїн, проникаючої (тобто
глибокої) корозії пружини підлягають вибраковуванню. Так само як і під час згину, не
перпендикулярності торців до осі, нерівномірності кроку витків і втрати
пружності більш допустимих значень.
Згин пружини та не перпендикулярність її торців до осі допускається не
більше 1,5–3,0% за довжину. Нерівномірність кроку витків допускається до 20%,
тобто різниця між найбільшим відхиленням від середнього значення і середнім
значенням не має перевищувати 20%. Ці параметри вимірюють з допомогою лінійки та
щупа чи з допомогою кутоміра і щупа на перевірній плиті.
Вимірювання зусилля, створюваного пружиною, здійснюють на спеціальних приладах (наприклад, МІП-100), або на нескладних пристроях, основними елементами яких мають бути лінійка та силовимірювальний засіб.
Рисунок 1.2.14 Прилад для випробування пружин МІП-100
Машина для випробування пружин МІП-100
Стенд для випробування пружин СТИ100
Рисунок 1.2.15 Приводні роликові ланцюги двох
типорозмірів
Рисунок 1.2.16 Конструкція втулко-роликового ланцюга: 1- зовнішні пластини; 2 -внутрішні пластини; 3 - валик; 4 – втулка; 5 - ролик (сепаратор)
У ланцюгових зірочках контролюють спрацювання зубів вимірюванням їх товщини штангензубоміром, діаметри посадкових отворів маточин і спрацювання шпонкових і шліцьових пазів.
Рисунок 1.2.17 Шпонкове з’єднання
Рисунок 1.2.18 Переріз шліцьового валу і втулки с прямокутним профілем
Шпонкові пази в інтервалі ширин 8–14 мм не повинні перевищувати
номінальні значення на 0,2–0,25 мм. Для їхнього контролю найкраще виготовити
граничний калібр-шпонку відповідної товщини.
Для прямобічних шліцьових пазів допустимі значення дещо більші, ніж для шпонкових, і становлять
0,30–0,40 мм.