Розділ 2
Розділ 2. Механічні випробування
матеріалів
Другий розділ посібника присвячений дослідженню механічних властивостей
і вивченню основних механічних характеристик матеріалів.
Механічні властивості матеріалів характеризують їх здатність опиратися
деформуванню і руйнуванню під дією зовнішніх сил та інших чинників. До основних
механічних властивостей матеріалів відносяться: міцність, пружність і
пластичність.
Міцністю називають здатність матеріалу чинити опір руйнуванню і утворенню
залишкових деформацій, пружність –
здатність матеріалу відновлювати свою форму і розміри після припинення дії
зовнішніх сил, пластичність – здатність матеріалу зазнавати
залишкові деформації.
Механічні властивості матеріалів характеризуються низкою величин, що
називаються механічними
характеристиками. У наведених лабораторних роботах визначаються
характеристики статичної міцності (границя пропорційності, границя текучості,
границя міцності (тимчасовий опір),
та істинний опір розриву), характеристики пластичності (відносне залишкове
подовження і відносне залишкове звуження після розриву), а також розглядається
поведінка пластичних і крихких матеріалів при розтягу, стиску, крученні і
ударі.
Для виконання робіт другого розділу посібника необхідно ознайомитись з
принципами дії та будовою випробувальних машин, приборів, пристроїв. Огляд
випробувальних машин і устаткування наведено у першому розділі. У тих випадках,
коли методику випробувань важко викласти окремо від опису машин або приладів,
цей опис наводиться у відповідній роботі.
Різноманіття умов експлуатації та обробки матеріалів надає необхідність
проведення великої кількості механічних випробувань, які можна класифікувати за
різними принципами. За характером зміни діючих на зразок навантажень розрізняють
статичні та динамічні
випробування.
Статичні випробування характеризуються плавним, відносно повільним (тривалістю від декількох секунд до
хвилини) зростанням навантаження на зразок від нуля до деякої максимальної
величини і, відповідно, з невеликою швидкістю деформації зразка.
Залежно від схеми прикладання навантаження на зразок розрізняють
наступні статичні випробування: одновісний розтяг і стиск, одновісний згин,
кручення, розтяг і згин зразка з надрізом.
Динамічні випробування характеризуються прикладенням до зразків
миттєвого навантаження з різкою зміною його величини і великою швидкістю
деформації зразка. Тривалість всього випробування не перевищує сотих або
тисячних часток секунди. В результаті динамічних випробувань зазвичай
визначається величина повної і питомої роботи динамічної деформації, а також
величина залишкової деформації зразка.
2.1. Лабораторна робота
Випробування
на розтяг маловуглецевої сталі
МЕТА РОБОТИ: дослідження властивостей та поведінки матеріалу при центральному
розтягу, побудування та аналіз діаграми розтягу, спостереження за деформацією
зразка до розриву.
Короткі теоретичні відомості
Випробування на одноосьовий статичний розтяг є найбільш поширеним способом механічних випробувань матеріалу, що пояснюється наступними його перевагами:
при
одноосьовому розтягу в зразку виникає однорідний напружений стан. Це означає, що
у всіх точках поперечного перерізу робочої частини зразка напруження однакові і,
незалежно від того, деформується зразок пружно або пластично, вони визначаються
за однією і тією ж формулою:
де F – навантаження, що розтягує, Н;
А0 – початкова площа
поперечного перерізу зразка, мм2.
Ø методика проведення
випробувань на розтяг не складна і добре відпрацьована;
Ø конструкції зразків і
захватів випробувальних машин прості і технологічні.
Спостерігання за поведінкою матеріалу i визначення його характеристик міцності і пластичності при
розтягу – один із основних i найбільш розповсюджених видів випробувань. Отримані в результаті експерименту
характеристики дозволяють зробити
висновки про міцність матеріалу при статичних навантаженнях, обирати
матеріал для конструкції, що
проектується i вважаються основними під час розрахунків деталей машин,
елементів конструкцій i споруд на
міцність.
Випробування на
статичний розтяг проводяться шляхом плавного безперервно зростаючого
навантаження зразка круглого або прямокутного перерізу на випробувальній машині
УИМ-50. При цьому процес деформування розвивається в такій послідовності: пружна
деформація, пружно-пластична деформація і руйнування.
При звичайній кімнатній температурі матеріали можна умовно поділити на
пластичні і крихкі. Пластичні матеріали руйнуються тільки після значних
залишкових деформацій, крихкі – при досить малих залишкових деформаціях. Такий
поділ, можна сказати, умовний, тому що, по-перше, не існує чіткої межі між
пластичними і крихкими матеріалами, і, по-друге, пластичні властивості матеріалу
змінюються залежно від певних умов.
До пластичних матеріалів відносяться: маловуглецева сталь, мідь, бронза
та ін.; до крихких: чавун, бетон, цегла та ін.
Для випробувань на
розтяг, відповідно до ГОСТ 1497-84 (ІСО 6892-84) застосовують пропорційні
циліндричні зразки діаметром d від 5 мм і більше (рис. 2.1, а,б,в) або плоскі (з листового матеріалу)
товщиною а від 0,5 мм і більше (рис. 2.1,
г).
Нормальна початкова розрахункова довжина зразка повинна
становити:
l0 =
10d0,
де d0
- початковий діаметр поперечного перерізу
зразка, d=10мм.
На рисунку 2.1 представлено 4 види стандартизованих
зразків:
Ø круглі з
довжиною l0 =15d0 - для зразків
п’ятнадцятиразової
довжини (рис. 2.1, а,);
Ø круглі з
довжиною l0 = 10d0 - для зразків
десятиразової довжини (рис.
2.1, б,);
Ø круглі з
довжиною l0 = 5d0 - для коротких
зразків (рис. 2.1, в,);
для прямокутних зразків з розмірами (a x b) (рис. 2.1, г,):
Найбільш розповсюджені випробування на циліндричних зразках (рис. 2.2, а). Після випробувань зразок видовжується на довжину ℓ1 і ми отримуємо зруйнований зразок, на якому є в наявності звужене місце (рис. 2.2,б), яке має назву «шийка». Воно може з’явитися у будь якій послабленій точці розрахункової довжині ℓ0 зразка, це залежить від кількох факторів, які обумовлюють умови виробництва зразка та ін. Зразок має на кінцях потовщення, так звані головки для захоплень випробувальною машиною.
Вибір форми та розмірів зразка обумовлюється можливостями виготовлення, а також потужністю і конструкцією випробувальної машини, що використовується. З метою економії матеріалу при масових випробуваннях доцільніше застосування коротких зразків п’ятикратної довжини, для випробувань яких застосовують машину УММ-5 (максимальне навантаження 5 тон). Але для того, щоб більш наочно спостерігати за зміною властивостей матеріалу рекомендують використовувати 10-ти кратний зразок. Для його випробувань використовують універсальну випробувальну машину УИМ-50 (максимальне навантаження 50 тон). На рисунку 2.3 представлений циліндричний зразок, який виконано з м’якої сталі.
Під час проведення випробувань за допомогою діаграмного апарату
випробувальної машини можна записати діаграму розтягу зразка, тобто залежність подовження зразка Δl від навантаження F.
Розрізняють три типи діаграм розтягу (рис. 2.4):
а) діаграма розтягу зразка з пластичного матеріалу, що має виражений
перехід з пружної області деформування в пружно-пластичну (рис. 2.4, а). На
діаграмі цей перехід відображається появою «площадки текучості», впродовж якої деформація в зразку зростає
практично без збільшення навантаження. Такий тип діаграми характерний лише для
деяких металевих сплавів (маловуглецеві сталі, деякі латуні, відпалені
марганцевисті і алюмінієві бронзи). Іноді на початку «площадки текучості» можна
спостерігати «зуб» плинності (показаний тонкою перервною лінією). Для цих
сплавів існує фізична границя текучості.
б) діаграма розтягу зразка з пластичного матеріалу, що має плавний
перехід з пружної області деформування у пружно-пластичну (рис. 2.4, б), яка
властива більшості чистих металів і металевих сплавів. Для них можна визначити
лише умовну границю текучості.
в) діаграма розтягу зразка з крихкого матеріалу (рис. 2.4, в), є характерною для сірих і білих чавунів, загартованих і не відпущених сталей, литих алюмінієвих і цинкових сплавів, а також багатьох неметалів: каменю, цегли, бетону, деяких пластмас та ін. Діаграма розтягу таких матеріалів коротка в напрямку подовжень, що ілюструє їх крихкість (невелику пластичність).
Основні властивості матеріалу визначають з діаграми розтягу, яка
будується в координатах F – Δℓ за допомогою пристрою,
що записує на випробувальній машині. Діаграма є наочним представленням того, що
відбувається з матеріалом усередині.
Для маловуглецевої сталі Ст. 3 приблизний обрис цієї діаграми наведено на рисунку 2.5.
Випробування проводять на універсальній випробувальній машині УИМ-50. На
ній можливо випробувати зразки на розтяг, стиск, згин. Масштаб запису
навантаження залежить від шкали, встановленої для проведення випробування.
Машину можна настроювати на максимальне навантаження 5, 10, 25 і 50 тон. Під час
проведення випробувань на розтяг встановлюється максимальне навантаження на
машині – 25 тон.
У такому випадку масштаб навантаження (в напрямку вертикальної осі F) становить
Масштаб запису деформації (в напрямку горизонтальної осі Δℓ) перед випробуванням приймається
рівним
Аналіз діаграми розтягу.
На етапі навантаження до деякої сили Fпц (точка A) спостерігається пряма пропорційна залежність між видовженням зразка i силою F, що його викликала і зворотна пропорційна залежність до площі поперечного перерізу А. Позначаючи через Δℓ приріст довжини від сили F, можемо записати формулу, що зв’язує ці дані, яка носить назву закону Гука:
де: Е – коефіцієнт пропорційності, який характеризує жорсткість
матеріалу і має назву модуль пружності
І-го роду або модуль Юнга, МПа;
А – площа поперечного перерізу зразка, мм2;
Δℓ – величина абсолютного видовження зразка:
Δℓ = ℓ1 - ℓ0, (2.2)
де: ℓ1 – довжина зразка після руйнування,
мм;
ℓ0 – початкова довжина зразка до руйнування,
мм.
Е∙А – добуток, характеризує
жорсткість стержня при розтягу (стиску).
Після розвантаження у точці А початкова довжина зразка відновлюється,
тобто деформація зникає. Ця властивість називається пружністю, а навантаження на ділянці ОА є навантаженням Fпц, що відповідає границі пропорційності σпц.
При подальшому навантаженні починається незначне відхилення від прямої
лінії. Якщо в точці В зупинити дослід, то після розвантаження деформація
практично зникає, тобто з’являється залишкова деформація, що складає
0,001-0,005%. Тому вважатимемо, що взагалі ділянка ОВ є ділянкою пружності, а сила
(точка В) називається навантаженням Fпр, що відповідає границі
пружності σпр.
При досягненні навантаженням деякого значення Fт (точка С) зразок видовжується («тече») без збільшення, а інколи i при
зменшенні навантаження. На діаграмі з’являється так звана «площина текучості».
На цій ділянці з’являється залишкова (пластична) деформація Δℓзал, а матеріал на
ділянці ВС проявляє властивість текучості.
Щоб зразок деформувався дедалі більше, потрібно збільшувати навантаження, матеріал знову здатний чинити опір розтягу. Пояснюється це явище зміцненням матеріалу. Якщо зразок повністю розвантажити, то пружна деформація Δℓпр зникне, а залишкова Δℓзал залишиться, перо самописа прокреслить пряму лінію ZО1 (рис. 2.5), яка буде паралельна пропорційній ділянці ОА. При повторному навантаженні, яке буде відразу після розвантаження, перо спочатку накреслить лінію О1Z, а зі збільшенням навантаження переміститься далі уздовж ділянки ZD. Властивості матеріалу змінюються: пластичні властивості погіршуються, а твердість підвищується. Відбуваються зміни в кристалічній решітці матеріалу, він зміцнює сам себе. Це призводить до появи явища об’ємного зміцнення. В одних випадках ці зміни корисні, в інших шкідливі i їx усувають. В результаті попередньої пластичної деформації метал стає більш міцним (явище наклепу), збільшується діапазон пружного розтягування. Пластичні властивості металу при цьому знижуються, зменшується також і його статична в’язкість. Остання обставина має велике значення для матеріалу, який піддається дії змінних напружень. Подальше збільшення навантаження призводить до появи «шийки» на зразку (точка D) – звуження в деякому одному місті зразка, i руйнуванню. До моменту появи шийки навантаження на зразок досягає свого максимального значення Fмц або Fтм і є навантаженням, що відповідає границі міцності σмц (рис. 2.6, а,б) або тимчасовому опору σтм.
До моменту розриву робоча частина зразка ℓ0 видовжилась на
величину загальної деформації Δℓзаг. Після розриву пружна частина загальної
деформації зникає, залишається тільки залишкова деформація Δℓзал. На місці утворення
«шийки» пepepiз зразка зменшився.
Руйнування крихких матеріалів відрізняється тим, що воно відбувається
вже при невеликих деформаціях (рис. 2.4,
в). При розтягу чавунного зразка, до моменту розриву виникають невеликі
деформації, руйнування відбувається раптово, величини відносного звуження і відносного подовження є дуже
малими. Як правило, крихкі матеріали погано опираються розтягу, їх границя
міцності має невелике значення в порівнянні з границею міцності пластичних
матеріалів. Якщо розглядати діаграму розтягу крихких матеріалів, то можна
зазначити, що вона не має чітко вираженої прямої лінії, яка є на ділянці
пропорційності для пластичних матеріалів (рис 2.5). Тому умовно прийнято
говорити, що крихкі матеріали не мають пружних властивостей, а тому і не
підкоряються закону Гука.
Оснащення робочого місця
v випробувальна машина
УИМ-50, підготовлена до проведення
експерименту;
v стальний зразок круглого перерізу;
v штангенциркуль ШЦ-0,1;
v
методичні вказівки до виконання лабораторної роботи;
v
калькулятор, олівець,
лінійка;
журнал лабораторних робіт.
Порядок виконання випробувань
Лабораторна робота проводиться у такій
послідовності:
1.
Розглянути зразки, які використовують для випробувань на
розтяг.
2. Виміряти штангенциркулем початковий діаметр d0 зразка і початкову довжину. Результати записати у журнал спостережень (табл.2.1):
1.
Перевірити готовність машини
для випробувань до експерименту,
настроїти силовимірювач на шкалу з максимальним навантаженням 250кН.
2.
Встановити зразок у затискачі випробувальної машини і налаштувати
діаграмний апарат.
3. Плавно навантажувати зразок з його розтягуванням до
розриву.
4.
Звільнити зразок з затискачів випробувальної
машини.
5.
Зі
шкали силовимірювача зняти значення навантаження, що відповідає границі міцності
Fмц (це значення навантаження на шкалі фіксується
стрілкою).
6.
Виміряти штангенциркулем діаметр зразка в місці розриву dш і робочу довжину
зразка l1 (для вимірювання dш і l1 обидві частини
розірваного зразка щільно стикуються за місцем розриву). Результати записати у
таблицю 2.1.
7.
Зняти
діаграму із записуючого пристрою та занести в журнал лабораторних робіт.
Обробити отриману діаграму розтягу:
-
зазначити характерні точки A, В, C, D, К;
-
надати
характеристики ділянок діаграми;
- визначити відповідне навантаження Fпц, Fпр, Fт, Fмц, Fр.
Для визначення навантаження Fi, що відповідає кожній точці машинної діаграми розтягу, необхідно виміряти ординату уi навантаження до відповідної точки в міліметрах та помножити на масштаб сил:
Руйнувальне навантаження (навантаження, що відповідає істинному опору розриву):
- результати розрахунків записати у журнал спостережень (табл. 2.2):
10.
Відповісти на контрольні запитання.
11.
Захистити лабораторну роботу у викладача.
Тестові запитання для самоконтролю
1. Яка одиниця вимірювання механічного напруження?
Н/м2;
Н/м;
Н/м3.
2.Яка одиниця вимірювання абсолютної деформації?
мм;
відсотки;
безрозмірна
величина.
3.Яка одиниця вимірювання
модуля поздовжньої пружності
матеріалу Е?
Н/м2;
Н/м;
Нм.
4.Як позначається відносне подовження?
ε;
∆ℓ;
Μ.
5.Як позначається абсолютна поздовжня деформація?
∆ℓ;
ε;
μ.
6.В яких координатних осях на випробувальній машині записується діаграма
розтягу?
F-∆ℓ;
σ-ε;
σ-∆ℓ.
7.Яка деформація називається пружною?
та, що зникає після розвантаження;
та, що залишається після розвантаження;
та, що не виникає при навантаженні.
8.Яка деформація називається пластичною?
та, що залишається після розвантаження;
та, що зникає після розвантаження;
та, що не виникає при навантаженні.
9.Чим характеризується «зона текучості» на діаграмі розтягу?
зростанням пластичної деформації без зростання
навантаження;
зростанням пружної деформації без зростання
навантаження;
зростанням пружної та пластичної деформацій.
10. Після якої точки на діаграмі розтягу (діаграма) з’являється залишкова деформація?
В;
D;
С.
11.Яка точка діаграми розтягу (діаграма) відповідає моменту появи
«шийки»
на зразку?
D;
В;
С.
12.Яка ділянка діаграми розтягу (діаграма) відповідає зоні зміцнення
матеріалу?
СD;
ОА;
ВС.
13. Яка ділянка діаграми розтягу (діаграма) відповідає зоні текучості
матеріалу?
ВС;
ОА;
СD.
14.До якої точки на діаграмі розтягу (діаграма) можна навантажувати зразок,
щоб після розвантаження довжина зразка не змінилась?
В;
D;
К.
15.Ординату якої точки діаграми розтягу (діаграма) треба визначити, щоб
розрахувати границю пропорційності?
А;
D;
С.
16.Ординату якої точки діаграми розтягу (діаграма) треба визначити, щоб
розрахувати границю пружності?
В;
D;
С.
17.Ординату якої точки діаграми розтягу (діаграма) треба визначити, щоб
розрахувати границю текучості?
С;
D;
В.
18.Ординату якої точки діаграми розтягу (діаграма) треба визначити, щоб
розрахувати границю міцності (тимчасовий опір)?
D;
В;
С.
19.При розрахунку механічних характеристик міцності (границя пропорційності,
границя пружності, границя текучості, тимчасовий опір) яка використовується
площа перерізу зразка?
початкова площа до навантаження;
та, що є у зразка в момент розриву;
площа шийки.
20.При розрахунку істинного опору розриву матеріалу, яка використовується
площа перерізу?
площа шийки;
початкова площа перерізу зразка;
площа, яка відповідає максимальному значенню сили.
2.2. Лабораторна робота
Випробування
на розтяг маловуглецевої сталі.
Основні механічні характеристики міцності та
пластичності
МЕТА РОБОТИ: визначення механічних характеристик міцності та пластичності при
розтягу м’якої сталі та встановлення марки
матеріалу, що
досліджували.
Короткі теоретичні відомості
Механічні характеристики матеріалів, які визначаються при випробуваннях
на розтяг, вважають основними. Однак в деяких випадках необхідно проводити
випробування і при інших видах навантаження: при стиску, крученні, згині, зсуві.
Крім статичних випробувань при нормальній температурі, проводяться також
випробування матеріалів в умовах динамічних навантажень (удар), випробування при
напружених, що змінюються циклічно, випробування при високих і низьких
температурах та інші.
Для забезпечення порівнянності результатів механічних випробувань
методика їх проведення і прийоми обробки отриманих даних регламентуються
відповідними стандартами (ГОСТ, ІСО).
Для вивчення основних механічних характеристик міцності існує діаграма
напружень (рис. 2.7), яка може бути отримана із діаграми розтягу зразка для
заданого матеріалу. Треба зазначити, що діаграма розтягу будується в осях F –
Δℓ і залежить від вихідних розмірів зразка, а тому характеризує
поведінку під навантаженням не тільки матеріалу, а й конкретного
зразка.
Тому накреслену на випробувальній машині діаграму розтягу (у
координатних осях F – Δℓ) перебудовують. По осі абсцис
нової діаграми відкладають відносні подовження ε
=Δℓ/ℓ, а по осі ординат – нормальні напруження σ, що діють в поперечному перерізі
зразка.
Отримана діаграма в осях σ – ε називається діаграмою умовних напружень при
розтягу. Обрис цієї діаграми для маловуглецевої сталі Ст.3 наведено на рисунку
2.7. Умовною її називають тому, що
при визначенні її абсцис враховується початкова робоча довжина зразка ℓ0, а при визначенні
ординат – початкова площа поперечного
перерізу зразка А0 (штрихова лінія на
рисунку 2.7). Вона не залежить від
початкових розмірів зразка і характеризує поведінку матеріалу, що випробується
при розтягу.
Однак у процесі розтягнення зразка впродовж часу змінюється і довжина зразка, і його площа поперечного перерізу. Враховуючи це зверху умовної діаграми будується істина діаграма напружень.
Істиною діаграмою називається діаграма, яка побудована з урахуванням зміни
розмірів поперечного перерізу, а саме діаметру зразка в «шийці» (суцільна лінія на рисунку
2.7) Аш.
Основні механічні характеристики міцності
Розглянемо істину і умовну діаграми напружень та визначимо основні механічні характеристики міцності.
На початку ділянки OA
діаграма являє собою похилу пряму. У цих межах нормальні напруження, що
виникають в поперечному перерізі зразка, зростають прямопропорційно до відносних
поздовжніх деформацій, тобто виникають пружні деформації, а це свідчить про те,
що матеріал підкоряється закону Гука (формула 2.2).
Тому напруження, вище якого матеріал перестає підкорятися закону Гука
називають границею
пропорційності
де Fпц – навантаження у зоні пружності (ордината точки А),
Н;
А0 – початкова площа
поперечного перерізу зразка, мм.
Поблизу точки A, але не набагато вище її, знаходиться точка B, що відповідає границі пружності.
Границею пружності
де Fпр – навантаження, що відповідає границі пружності
(ордината точки В), Н.
Прийнято вважати, що до границі пружності в матеріалі є тільки пружні
деформації, при напруженнях більших за границю пружності – пружні і залишкові
деформації. У зв’язку з тим, що точка B розташована поряд із точкою А, то нею
надалі нехтують.
Вище точки А деформації зростають швидше напружень і діаграма
викривляється, тобто закон Гука порушується. Таким чином, закон Гука
спостерігається тільки до границі пропорційності.
Починаючи від точки А і до точки С діаграма має горизонтальну (або майже горизонтальну) ділянку. На ділянці АС деформації збільшуються без збільшення напружень. Якщо уважно стежити за стрілкою силовимірювача випробувальної машини, то по досягненню площадки текучості (точка C діаграми) вона деякий час залишається нерухомою. Після розвантаження на зразку є в наявності значна залишкова деформація. Точка C відповідає границі текучості, яка визначається як відношення:
де Fт – навантаження площадки текучості
(ордината точки С), Н.
Границею текучості = 240 МПа). Деякі пластичні матеріали, наприклад, дюралюміній, не мають
на діаграмі розтягу «площадки текучості». Для таких матеріалів вводиться умовна
границя текучості.
Умовна границя текучості σ0,2 – це напруження, що
відповідає відносній залишковій деформації, яка дорівнює
0,2%.
Після проходження «площадки текучості» при подальшому збільшенні відносної деформації напруження (а отже, і сила, що розтягує) знову збільшуються (рис. 2.7), матеріал знову здатний чинити опір розтягуванню. Відбувається як би «самозміцнення» сталі, і діаграма змінюється по плавній кривій з найвищою точкою D. Подальше збільшення навантаження призводить до появи «шийки» на зразку, а точка D відповідає границі міцності – тимчасовому опору розриву.
Границею міцності = 400
МПа):

де Fмц –
максимальне навантаження (ордината точки D), Н.
Напруження і
це зменшення незначне, тому
умовність цих характеристик зазвичай не обмовляється.
До того, як розтягування досягне границі міцності поздовжні і поперечні
деформації зразка рівномірно розподіляються по всій його розрахунковій довжині.
Після досягнення границі міцності ці деформації концентруються в одному найбільш
слабкому місці. Тут з’являється значне місцеве звуження, утворюється так звана
«шийка»
Істинним опором розриву називається напруження, що визначається відношенням навантаження Fр в момент розриву до площі поперечного перерізу шийки Аш в місці розриву:
де Fр – навантаження при розриві зразка
(ордината точки К), Н.
При розрахунках інженерних конструкцій використовують в основному
границю текучості та границю міцності. Визначені у роботі напруження, що
відповідають границі пропорційності та істинному опору розриву зразка (умовні і
справжні), не характеризують властивості міцності матеріалу і тому мають чисто
теоретичний інтерес.
Характер руйнування зразка. Механізм руйнування починається в області шийки з утворення дрібних
пустот – пор, витягнутих у подовжньому напрямі (рис. 2.8). Під дією напружень,
що розтягують, матеріал перемичок між порами руйнується, пори зливаються, у
результаті чого з’являється центральна тріщина у напрямку, перпендикулярному осі
розтягування.
Утворення тріщини поблизу центру перерізу пояснюється тим, що в цій зоні внаслідок виникнення неоднорідного напруженого стану, при якому нормальні напруження досягають на осі зразка максимального значення σmax, матеріал має знижену здатність до пластичної деформації. Це в значній мірі сприяє початку руйнування зразка, яке на цій стадії має крихкий характер. Однак в іншій частині поблизу поверхні матеріал продовжує розтягуватися пластично. Потім тріщина починає поширюватися в обидві сторони у напрямку до поверхні, утворюючи злам. Збільшення розмірів тріщини відбувається за рахунок подальшого приєднання нових пустот у результаті розриву перемичок і раніше утворюваної центральної зони тріщини. Процес розвитку тріщини супроводжується концентрацією напружень біля вершини (вістря) тріщини.
При наближенні тріщини до поверхні створюються умови, при яких вона
повертається під кутом, рівним приблизно 450, до початкового напрямку
поширення і, виходячи на поверхню, утворює конічну частину зламу. У цій стадії
процес відбувається за механізмом, який багато в чому аналогічний розшаруванню у
площинах ковзання або зісковзування. У зразку утворюються мікроскопічні
нерівності, що виникають у наслідок незворотних зрушень, які відбуваються в
кристалах під дією найбільших дотичних напружень τmax.
Основні механічні характеристики пластичності
Ступінь пластичності матеріалу може бути охарактеризована величинами
відносного залишкового подовження зразка, доведеного при розтягуванні до
розриву, і відносного залишкового звуження шийки зразка в момент розриву. Чим
більше ці величини, тим пластичніше матеріал. До моменту розриву робоча частина
зразка ℓ0 видовжилась на величину загальної деформації
Δℓзаг.
Відношення приросту подовження зразка Δℓ до його початкової довжини ℓ0 називають відносним залишковим подовженням ε, або поздовжньо(е)ю деформацією:
де Δℓ – абсолютне видовження зразка, мм. Визначається як абсолютна різниця між довжиною зразка після випробування ℓ1 і до випробування ℓ0:
ℓ0
– початкова довжина зразка, мм.
де ΔА – абсолютне звуження
зразка, ΔА = А0 - Аш, мм2.
Відносне залишкове подовженням та відносне залишкове звуженням є
безрозмірними величинами, тому оцінюються у відсотках.
Як ε, так і ψ характеризують пластичність
матеріалу при розтягу, тобто його здатність отримувати залишкові деформації до
руйнування. При великих значеннях ε і ψ матеріал вважається пластичним,
при малих (зазвичай при ε <1%) –
крихким.
Закон Гука
Сучасне трактування закону Гука належить Луї Нав’є, який встановив, що
напруження і деформації матеріалу в точці пов’язані
співвідношенням:
де σ – нормальні напруження,
що відповідають пропорційній ділянці діаграми (границя пропорційності),
МПа;
E – модуль пружності
матеріалу І-го роду при розтягу, МПа;
ε – відносна лінійна деформація, що
відповідає ділянці пропорційності.
Тангенс кута нахилу
Кут нахилу ділянки пропорційності , тим міцніший матеріал, чим менше
, тим м’якіше.
Для найбільш поширених матеріалів Е має наступні значення:
сталь – (2,0-2,1)·105МПа;
мідь – 1,2·105 МПа;
алюмінієво-магнієві сплави – (0,7-0,8)·105
МПа;
дерево (вздовж волокон) – (0,08-0,12)·105 МПа;
вапняк, граніт – (0,4-0,5)·105 МПа.
Вперше поняття про модуль поздовжньої пружності ввів у 1820 р. Томас
Юнг, який визначив його чисельне
значення для сталі, чавуну, міді і ряду інших матеріалів. Тому модуль
поздовжньої пружності називають ще модулем Юнга (а також модулем пружності І-го
роду).
Розглянемо формулу (2.2)
закона Гука: якщо обидві її частини розділити на ℓ,
отримаємо:
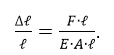
Зробимо необхідні перетворення: права частина це є відносне видовження ε, в лівій частині відношення F/A це є напруження σ, отримаємо інший вираз закону Гука через відносну деформацію:
Таким чином нормальне напруження σ при розтягу (стиску)
прямопропорційне відносному видовженню ε з урахуванням коефіцієнта
пропорційності Е, яким є модуль
Юнга.
Для проведення перевірочного розрахунку необхідно знати значення допустимих напружень, після перебільшення яких конструкція втрачає міцність. Для забезпечення працездатності конструкції у разі статичних навантажень пластичного матеріалу допустиме нормальне напруження визначають як відношення небезпечного напруження до коефіцієнту запасу міцності. Для пластичних матеріалів визначається за формулою:
де
– коефіцієнт запасу міцності відносно границі
текучості:
=
1,5…2,0.
де
– коефіцієнт запасу міцності відносно границі
міцності:
=
3… 5
Оснащення робочого місця
v стальний зразок круглого перерізу, та зразок, що було розірвано при
виконанні лабораторної роботи №1;
v
методичні вказівки до виконання лабораторної роботи;
v
калькулятор, олівець, лінійка;
v
журнал лабораторних робіт.
Порядок виконання випробувань
Лабораторна робота проводиться у такій
послідовності:
1.
Перенести в журнал лабораторних робіт діаграму розтягу зразка,
перетворивши її у координатні осі σ – ε (умовна діаграма).
2. Зверху умовної діаграми побудувати істину діаграму напружень.
3. Використовуючи результати попередньої лабораторної роботи визначити механічні характеристики міцності м’якої сталі і розрахунки занести у журнал спостережень (табл. 2.3).
4. Визначити значення механічних характеристик пластичності і розрахунки занести в журнал спостережень (табл. 2.4).
5.
По діаграмі напружень
встановити небезпечне напруження:
небезпечним напруженням вважається таке напруження, при якому виникають
залишкові деформації. Із аналізу діаграми м’якої сталі (рис.2.7) таким
напруженням є границя текучості
6.
Аналізуючи визначені значення механічних характеристик та
використовуючи довідкову літературу
(див. Додаток1) встановити марку
сталі.
7.
Розрахувати допустимі напруження.
8.
Визначити модуль пружності І-го роду (модуль
Юнга).
9.
Встановити і описати характер руйнування зразка у місці розриву: при
розтягу зразка руйнування відбувається відриванням зі зсувом (рис. 2.8). Причому
відрив частинок відбувається по центральній частині поперечного перерізу шийки
(під дією нормальних напружень σ) інша частина сколюється під кутом
450, з утворенням по периметру перерізу характерного віночка (зсув –
під дією дотичних напружень τ) Така форма руйнування
спостерігається тільки у пластичних матеріалів.
10.
Відповісти на контрольні запитання.
11.
Захистити лабораторну роботу у викладача.
Тестові запитання для самоконтролю
1. Чому діаграму розтягу зразка в координатах σ-ε називають умовною?
при розрахунках σ та ε не враховують зміну площі
перерізу;
при розрахунках σ та ε не враховують зміну довжини
зразка;
при розрахунках σ та ε не враховують зміну як довжини так і
площі перерізу зразка.
2. Що можна сказати про механічні характеристики матеріалу (діаграма 2) у
порівнянні з маловуглецевою сталлю (діаграма 1)?
матеріал більш міцний;
матеріал більш пластичний;
матеріал як більш пластичний так і більш міцний.
3. Що можна сказати про механічні характеристики матеріалу (діаграма 2) в
порівнянні з маловуглецевою сталлю (діаграма 1)?
матеріал більш пластичний;
матеріал більш міцний;
матеріал менш пластичний та менш міцний.
2.3. Лабораторна робота
Випробування
на СТИСК
СТАЛІ, ЧАВУНУ ТА ДЕРЕВА.
МЕТА РОБОТИ: дослідження поведінки сталі, чавуну і дерева при стиску та визначення
основних механічних характеристик міцності.
Короткі теоретичні відомості
Випробування на стиск проводять для визначення здатності матеріалів
чинити опір стискаючому навантаженню. Відносяться до числа найбільш поширених
випробувань, особливо для крихких матеріалів. Випробування проводяться на
зразках з круглим або квадратним поперечним перерізом, розміри яких визначаються
відповідно до ГОСТ 25.503-97 «Расчеты
и испытания на прочность. Методы механических испытаний металлов. Метод
испытания на сжатие».
Напруження і деформації при осьовому стиску визначаються так само, як і
при розтягу. Тому всі механічні характеристики, які визначаються при
випробуванні на стиск, зберігають ті ж визначення, що і при розтягу. Однак між
процесом деформування матеріалу при стиску і при розтягу є суттєва відмінність,
яке особливо проявляється при навантаженні зразка з пластичного матеріалу за
межами пружності.
Випробування на стиск є основними при визначенні механічних
характеристик крихких матеріалів, таких, як чавун, дерево, будівельні матеріали,
тощо. На відміну від випробувань на розтяг випробування на стиск мають наступні
особливості:
Ø в
процесі випробування пластичні матеріали можуть стискатись, не руйнуючись, а
крихкі – руйнуються;
Ø характеристики міцності і пластичності циліндричного зразка при
випробуваннях на стиск суттєво залежать від відношення висоти зразка до його
діаметра;
Ø на
результати випробувань значно впливають умови тертя по торцях зразка, які
перешкоджають появі поперечної деформації, і циліндричний (або призматичний)
зразок набуває бочкоподібну форму.
Під дією стискаючого навантаження різні матеріали ведуть себе по
різному. Тому для випробувань на стиск використовуємо дві групи матеріалів
ізотропні та анізотропні, а також два види зразків за властивостями: пластичні і
крихкі.
Ізотропними називаються матеріали, які мають однакові фізичні властивості у всіх напрямках. Для
випробувань на стиск в якості ізотропного матеріалу використовується сталь, як
пластичний, і чавун, як крихкий матеріал. Зразки з них виготовляють циліндричної
форми відповідно до ГОСТ 25.503-97
з відношенням висоти до діаметру 1≤ h/d ≤ 2. В даній роботі використовують зразки із розмірами ℓ =
Матеріали, властивості яких змінюються
залежно від напрямку, називають анізотропними. До таких матеріалів відносять такі матеріали, волокна
яких орієнтовані в певних напрямах – однонаправлені, шаруваті і
трьохмірноармовані.
Для випробувань за анізотропні матеріали використовують дерев’яні зразки
кубічної форми із розмірами (рис. 2.10). Залежно від розташування волокон їх випробують уздовж
волокон та упоперек.
Випробування на стиск проводять на універсальній випробувальний машині УИМ-50. Зразок встановлюють на опорну плиту нижньої траверси машини, притискаючи його до верхньої опорної плити (рис. 2.11) таким чином, щоб навантаження прикладалось строго уздовж осі зразка. Нижня траверса переміщується тільки уверх, утворюючи стискаюче зусилля.
Випробування пластичного матеріалу. Сталь.
На початку завантаження до деякого навантаження Fпц (рис. 2.12, а)
діаграма напружень при стиску малоувуглецевої пластичної сталі так само, як і
діаграма розтягу, являє собою похилу пряму ОА. Спостерігається пропорційна
залежність між деформацією i навантаженням, що викликало її. Це свідчить про
наявність пружних властивостей матеріалу. Потім діаграма закругляється і
переходить у ділянку з найбільшим нахилом до горизонталі – ділянку текучості АВ.
При стиску «площина текучості» не виходить настільки яскраво вираженою, як при
розтягу.
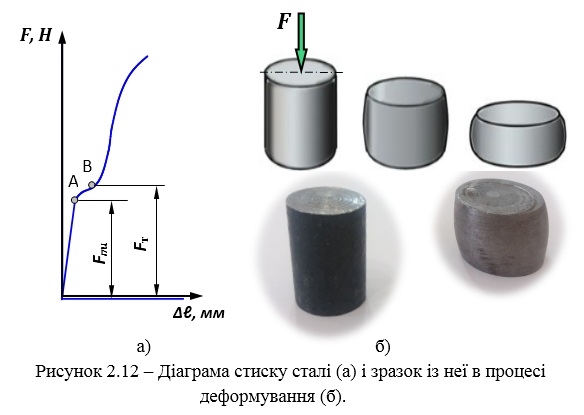
Кінцева точка діаграми стиску сталі відповідає не руйнуванню, як при
розтягу, а просто закінченню випробування. Зразок зі сталі при стиску не
руйнується. Закінчення випробувань (кінцева деформація стиску) визначається
можливістю машини.
Так само, як при випробуванні на розтяг, при стиску аналізується
діаграма стиску, яка може бути записана за допомогою діаграмного апарату
випробувальної машини в координатах: стискаюча сила F
– абсолютне укорочення Δℓ. При випробуванні на стиск мають місце лише дві характеристики
міцності: границя пропорційності σпц та границя текучості
σт.
Навантаження, що відповідає границі пропорційності Fпц та границі текучості Fт визначаються за тією ж методикою, що описана у попередніх лабораторних
роботах (лабораторна робота №1 і №2).
За границею пропорційності σпц спостерігається
незначне збільшення деформації, тобто, матеріал «тече», але без явно вираженої
площини текучості. Зразок приймає
бочкоподібну форму (рис. 2.12,б) внаслідок наявності тертя між торцями зразка i
поверхнями стискаючих плит.
Сили тертя, що виникають по торцях зразка, перешкоджають поперечній
деформації, і циліндричний (або призматичний) зразок набуває бочкоподібну форму.
Для зменшення бочкоподібності існує кілька прийомів. Найпростіший з них –
зниження сил тертя за рахунок шліфування торців зразків та їх змащення,
наприклад, графітом.
Пластичні і крихкі матеріали по-різному поводяться при стисненні. У
пластичних матеріалів границя пропорційності, а також фізична границя текучості
виявляються досить близькими до відповідних значень, що отримані при розтягу.
Тому вважається, що пластичні матеріали однаково працюють на розтяг і стиск. При стиску за границею
текучості внаслідок інтенсивного поперечного розширення зусилля, яке необхідне
для подальшої деформації зразка, швидко зростає. При цьому досить пластичні
матеріали при стиску не руйнуються, а розплющується під дією нормальних
напружень. Тому визначити границю міцності не можливо. Чітко виражена тільки
границя пропорційності.
Випробування крихкого матеріалу. Чавун.
Зразок з крихкого матеріалу при стиску може набувати бочкоподібну форму
лише у дуже незначній мірі. Процес навантаження закінчується руйнуванням зразка
– зсув під дією дотичних напружень τ. За руйнівного навантаження
визначається тимчасовий опір (границя міцності) при стиску τмц. Для крихких
матеріалів випробування на стиск є основним видом випробувань. Зауважимо, що
границя міцності при розтягу у крихких матеріалів істотно менша, ніж при стиску,
тобто крихкі матеріали краще чинять опір стиску.
Однак в умовах тих невеликих деформацій, при яких матеріал
використовують у різних деталях машин і споруд, діаграма F-Δℓ являє собою лінію малої кривизни (рис. 2.13, а), тобто відхилення від
закону Гука незначне. Тому у практичних розрахунках вважають, що матеріал
підкоряється закону Гука, а значення модуля пружності Е постійним.
Із аналізу діаграми видно, що чітко виражене тільки руйнівне навантаження Fмц, що відповідає границі міцності. Воно, до того ж, є максимальним. Відношення Fмц до початкової площі А0 поперечного перерізу називають границею міцності σмц (тимчасовим опором σтм) чавуну при стиску:
Зразок, укорочуючись (рис. 2.13, б), приймає бочкоподібну форму. Це
свідчить про наявність невеликих пластичних деформацій. При стиску зразків
відбувається ряд явищ, які суттєво відрізняють випробування на стиск від
випробувань на розтяг. При зменшенні висоти стиснутого зразка і переміщенні
часток у радіальному напрямку між торцями зразка й плитами преса виникають сили
тертя, спрямовані у бік, протилежний напрямку поперечної деформації, тобто
радіально до центру. Ці сили тертя порушують одновісний характер деформації
зразка.
Випробування показують, що руйнування чавунних зразків відбувається
шляхом зсуву по площині, нахиленої до осі зразка приблизно на кут α = 45°, тобто, по перерізу, де
діють максимальні дотичні напруження τ.
При руйнуванні навантажувальна здатність чавуну падає практично
миттєво, що характерно для крихких матеріалів. Границя міцності чавуну зазвичай досягає 500-1000 МПа.
Слід пам’ятати, що значення τмц значно залежить від
умов випробування i відношення висоти h до діаметра d зразка. Навіть вигляд
руйнування крихких матеріалів залежить від відношення висоти до
діаметра.
Границя міцності
крихкого матеріалу при стиску в декілька разів більша за границю міцності при
розтягу. Модулі пружності при розтягу та стиску також
різні.
Необхідно відмітити, що зазвичай крихкі матеріали опираються стиску
краще ніж розтягу. Це в значній мірі обмежує область їх застосування.
Випробування дерева.
Випробування дерев'яного зразка як представника анізотропних
матеріалів проводять уздовж (рис. 2.10, а; 2.11, б) i упоперек (рис. 2.10, б;
2.11, в) волокон. Отримані діаграми стиску (рис. 2.14) різко відрізняються одна
від одної.
Діаграма F-Δℓ стиску зразка уздовж волокон (рис. 2.14, а), зовні
схожа на діаграму стиску чавуну. Дубовий зразок, що випробують уздовж волокон на
стиск до руйнування, зазнає порівняно невеликих пластичних деформацій. Між силою
F i деформацією Δℓ на початку навантаження
спостерігається незначна нелінійна залежність, причому нелінійність зростає
у міру збільшення навантаження. Після досягнення граничного навантаження Fмц зразок починає
руйнуватися шляхом сколювання, що супроводжується характерним тріском (рис.
2.14, а – зигзагоподібна ділянка) з подальшим зменшенням навантаження.
Відношення навантаження, що відповідає границі міцності Fмц до початкової площі Ао поперечного перерізу зразка
називають границею міцності σмц. Ця характеристика
визначається за методикою, наведеною у попередніх лабораторних роботах (№1 і
№2).
У звичайних умовах руйнування відбувається шляхом зсуву однієї
частини зразка відносно другої
(рис. 2.15, а).
Момент втрати несучої властивості зафіксувати немає можливості.
Тому за руйнівну силу приймають умовно таку силу F/мц, при дії якої деформація (ущільнення) зразка по висоті досягає 1/3 початкового значення, тобто Δℓ=1/3h0 (рис. 2.14, б).
Відношення F/мц до А0 називають умовною границею міцності σ/мц дерева при стиску поперек волокон:
Порівнюючи діаграми стиску дерева уздовж і упоперек волокон з’ясовується, що при стиску до руйнування уздовж волокон зразок має значно менші деформації, ніж при стиску поперек волокон, характер руйнування в обох випадках різний. Міцність зразка в першому випадку в 7...10 разів вище, ніж у другому. Коефіцієнт анізотропії, що характеризує різні механічні властивості дерева уздовж i поперек волокон, являє собою відношення границі міцності при стиску уздовж волокон до границі міцності при стиску поперек волокон:
Таким чином крихкі й пластичні матеріали мають різні протилежні
властивості у відношенні їх опору простому стиску або розтягу. Крихкі матеріали
погано опираються розтягу і удару, чутливі до місцевих напружень. Пластичні матеріали таких недоліків не
мають, тому пластичність є одним із найважливіших якостей матеріалу. Крихкі
матеріали зазвичай дешевші і мають високу границю міцності при стиску, тому
можуть бути використані при статичному навантаженні.
При визначенні допустимих напружень крихких матеріалів за небезпечне
напруження приймають границю міцності
де
– коефіцієнт запасу
міцності відносно границі міцності:
=
3,0…5,0.
Значення коефіцієнта запасу міцності залежить від характеру
навантаження, властивостей матеріалу, розрахункової схеми, методу розрахунку,
тощо.
Оснащення робочого місця
v машина
УИМ-50, підготовлена до проведення
експерименту;
v стальний і чавунний циліндричні зразки;
v дерев’яні кубічні зразки – 2 шт.;
v штангенциркуль;
v
методичні вказівки до виконання лабораторної роботи;
v калькулятор, олівець, лінійка;
v
журнал лабораторних робіт.
Порядок виконання випробувань
Робота проводиться на сталевих, чавунних і дерев’яних зразках. Сталеві і
чавунні зразки – циліндричної форми, дерев’яні – кубічної. Дерев’яні і чавунні
зразки доводяться до руйнування, сталеві не руйнуються. Дерев’яні зразки
випробовують уздовж і поперек волокон.
Лабораторна робота проводиться у такій
послідовності:
1.
Перед
проведенням досліджень перевірити
підготовку випробувальної машини до проведення випробувань.
2.
Зробити заміри зразків. Результати вимірювань фіксують у таблиці
2.5.
1.
Проконтролювати налагодження шкали силовимірювача перед проведенням
досліджень. Сталь і дерево уздовж волокон випробують при максимальному навантаженні Fmax =
250кН, масштаб навантаження на діаграмному апараті
становить
. Дерево поперек волокон випробують при максимальному навантаженні Fmax
= 100кН,
масштаб навантаження становить
.
Масштаб запису деформації (в напрямку горизонтальної осі Δℓ) перед випробуванням приймається
рівним 2.
На
опорну плиту нижньої траверси машини послідовно встановити зразки та притиснути
до верхньої опорної плити.
Увімкнути машину і прикласти повільне навантаження (чавунний та дерев’яний
зразки доводять до руйнування).
3.
За
шкалою силовимірювача фіксується відповідне навантаження: для сталевих зразків
навантаження, що відповідає границі пропорційності Fпц і
границі текучості Fт, для
чавунних і дерев’яних навантаження, що відповідає границі міцності Fмц.
4.
Занести в журнал лабораторних робіт діаграми стиску зразків, що
випробувались.
5.
Зробити аналіз отриманих діаграм, визначити відповідно до кожного виду
матеріалу механічні характеристики міцності.
Провести необхідні розрахунки та результати занести у таблиці 2.6 і 2.7.
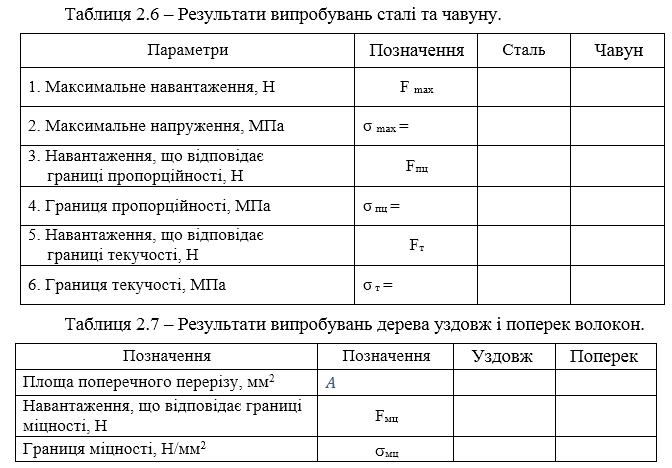
9.
За даними діаграми стиску встановити небезпечне напруження для кожного
виду матеріалу. Для
сталі небезпечним напруженням вважається границя текучості для дерева поперек волокон –
умовна границя міцності
, яку визначають при стиску зразка на 1/3 висоти
. Якщо висота зразка становить 40 мм, то 1/3 від 40 дорівнює 13,3мм.
Відкладаємо це значення на осі абсцис (абсолютна деформація зразка Δℓ) з урахуванням масштабу, від цієї
точки проводимо вертикаль уверх до перетинання з лінією діаграми. Таким чином
знаходимо положення точки В (рис. 2.14, б), що відповідає умовному навантаженню
по границі міцності
10.
Розрахувати допустимі напруження для досліджуваних
матеріалів.
11.
Встановити і описати характер руйнування зразків.
12 Відповісти на контрольні
запитання.
13. Захистити лабораторну роботу у викладача.
2.4. Лабораторна робота
ВИПРОБУВАННЯ НА КРУЧЕННЯ СТАЛІ ТА
ЧАВУНУ
МЕТА РОБОТИ: дослідження поведінки сталі й чавуну при крученні та визначення основних
характеристик міцності.
Короткі теоретичні відомості
В інженерній практиці на кручення в основному працюють деталі круглого
поперечного перерізу: вали, витки пружин і т.п.
Крученням називається деформація стержня (вала) під дією пар сил (моментів),
розташованих у площині, що перпендикулярна до осі вала, при додержанні умови
рівноваги. Ці пари сил називаються
моментами, що скручують М. При
крученні у поперечних перерізах вала виникають внутрішні силові фактори –
крутильні моменти Мкр.
В теорії кручення
круглих валів, що виготовлені із однорідного пружного матеріалу прийняті
наступні припущення:
1)
гіпотеза плоских перерізів: поперечні перерізи, що були плоскі до
деформації, залишаються плоскими і після скручування вала, лише зсуваються один
відносно другого на деякий кут γ (кут зсуву);
2)
вісь
вала не
викривляється;
3)
відстані між поперечними перерізами не змінюються, тобто відсутні
поздовжні деформації волокон
вала;
4) радіуси поперечних перерізів залишаються прямими й тільки обертаються на деякий кут φ – кут закручування.
Таким чином, кручення можна розглядати як чистий зсув, викликаний поворотом одного перерізу відносно другого. При цьому в поперечних перерізах виникають тільки дотичні напруження τ, які перешкоджають скручуванню валів і діють в площині перпендикулярній до осі вала:
де
Wр – полярний момент опору, мм3.
Полярний момент опору є геометричною характеристикою перерізу вала (залежить від діаметра d), для круглого перерізу визначається за формулою:
У будь-якому похилому перерізі виділеного елемента вала будуть діяти
нормальні і дотичні напруження. Найбільші нормальні напруження діють на головних
площадках, які, як відомо, нахилені під кутом 450 до утворюючої.
Таким чином, при крученні круглих валів небезпечними можуть бути як
дотичні напруження, що виникають у поперечних і поздовжніх перерізах вала, так і
нормальні напруження, що виникають у площині під кутом 450 до перших.
У зв’язку з цим, характер руйнування зразка буде залежати від здатності
матеріалу чинити опір дії дотичних і нормальних
напружень.
Розрахунковою довжиною вважають довжину циліндричної частини зразка ℓ0, на якій проводять
вимірювання кутової деформації (рис. 2.16), зазвичай довжина приймається ℓ0=10d. Випробування зразків з металопродукції діаметром менше 5 мм
проводяться тільки з урахуванням вимог стандартів на ці види
продукції.
Допускається випробування зразків і виробів, пропорційних нормальним, а
також трубчастих зразків.
Форма і розміри головок зразка визначаються способом кріплення у затискачах випробувальної машини.
При крученні, так як нормальні і дотичні напруження дорівнюють між собою, руйнування зразка може статися при досягненні ними граничного значення. Так як опір зсуву і відриву у різних матеріалів неоднаковий, руйнування зразків буде відбуватися по-різному (рис. 2.17). Так, сталевий зразок руйнується від зсуву по поперечному перерізу (рис.2.17, а), чавунний – відривом по гвинтовій поверхні з кутом нахилу 450 до осі зразка (рис.2.17, б).
Випробування на кручення поводять на спеціальних машинах, які забезпечують надійне центрування, плавність навантаження і відсутність згинаючих зусиль, також із можливістю достатньо точно задавати і вимірювати крутильні моменти і кути закручування.
У лабораторії кафедри є в наявності крутильна машина КМ-50, яка
призначена для випробувань на кручення з максимальним крутильним моментом
500Н·м. Машина має механічний привод. Шкала силовимірювача може настроюватись на
три види навантаження 100, 200 і 500Н·м. Для проведення досліджень стального та
чавунного зразків машину настроюють на максимальний крутильний момент
200Н·м.
На зразку проводять крейдою пряму лінію, і встановлюють його в затискачі крутильної машини (рис. 2.18, а). В процесі випробувань пряма лінія перетворюється в спіральну і, залежно від пластичних властивостей матеріалу, має відповідну кількість витків. На рисунку 2.18, б показана спіральна лінія для зразка зі сталі Ст.3, яка утворилася в результаті закручування. Така процедура проводиться для того, щоб можна було наявно побачити деформацію зразка.
Випробування на кручення відрізняються тим, що під час закручування
форма і розміри зразків не змінюються. Тому деформацію зразка наочно побачити
неможливо, наприклад, як це було при розтягу (рис.2.2,б), або стиску (рис. 2.12,
б; рис. 2.13, б; рис. 2.15).
де
ℓ – довжина ділянки, що підлягає закручуванню, м;
G – модуль пружності ІІ роду (модуль зсуву) – характеризує жорсткість
матеріалу при зсуві, МПа;
–
полярний момент інерції поперечного перерізу вала.
Тільки до цієї стадії навантаження справедливі формули для визначення величини дотичних напружень в будь-якій точці поперечного перерізу і на поверхні зразка, яка відображає закон розподілу напружень по діаметру перерізу вала:
де
Про пластичні властивості матеріалу можна судити за величиною відносної деформації – відносний кут закручування Θ, який визначається експериментально:
і являє собою відношення повного кута закручування
Процес деформації зразка при крученні наочно відображає діаграма
залежності абсолютного кута закручування φ від крутильного моменту М, яка будується
за допомогою діаграмного апарату випробувальної машини
КМ-50.
Випробування пластичного матеріалу. Сталь.
Аналогічно іншим статичним випробуванням матеріалів (розтяг, стиск та ін.) при крученні
визначають характеристики міцності та пластичності. Для цього будують діаграму
кручення в координатних осях М-φ. При чому, вісь φ повертається на кут α відносно свого горизонтально положення φ/ (рис. 2.19). Цей поворот властивий саме
випробувальній машині КМ-50 і враховує люфт затискача в момент увімкнення
установки.
Розглянемо діаграму кручення м’якої сталі (рис. 2.19). Вона не має виступів або переходів, які характерні діаграмі розтягу (рис. 2.5), а складається з плавної кривої з переходом у прямолінійну ділянку.
На початку навантаження (рис. 2.19) діаграма кручення пластичної сталі
так само, як і діаграма розтягу, являє собою похилу пряму ОА, це свідчить про
наявність пружних властивостей матеріалу. Навантаження до точки А – це
крутильний момент, що відповідає границі пропорційності Мпц.
Відношення Мпц до полярного моменту опору перерізу Wρ називається границею пропорційності сталі при крученні:
Після точки А діаграма закругляється і переходить у ділянку АВ – ділянку текучості. Але межа цієї ділянки на діаграмі ні як не виражена. Для знаходження границі текучості необхідно знайти положення точки В, яка обмежує «площину текучості». Це можливо зробити графічним способом.
Відкладаємо на похилій осі φ/ діаграми, що побудована за допомогою самописного пристрою випробувальної машини, відрізок ОО1, який дорівнює значенню кута закручування з урахуванням допуску на залишковий зсув 0,3% і відповідає границі текучості:
де
r – радіус перерізу зразка,
м;
– відносний залишковий зсув,
=0,003.
Із точки О1 проводимо лінію, яка паралельна пропорційній
ділянці діаграми ОА, до перехрестя з графіком залежності М-φ в точці В.
Ордината точки В буде відповідати крутильному моменту по границі текучості Мт. Відношення Мт до полярного моменту опору перерізу Wρ називається границею текучості сталі при крученні:
Кінцевої точки діаграма кручення для маловуглецевої сталі не має, тому
що кут закручування φ на стільки великий, що повна
діаграма уздовж осі абсцис не вміщується на діаграмному апараті. Зразок зі сталі
руйнується зсувом під дією дотичних
напружень τ (рис. 2.20, б). У момент
руйнування машина автоматично вимикається.
Значення крутильного моменту, при якому відбувається руйнування фіксується нерухомою стрілкою на силовимірювачу.
Значення повного кута закручування знімаємо з лімбу, що розташований в нижній частині випробувальної машини (рис. 2.21).
Пластичні і крихкі матеріали по-різному поводять себе під час кручення.
Сталь, як пластичний матеріал закручується на декілька обертів відносно
нерухомого перерізу. Неозброєним оком цю деформацію побачити неможливо.
Вимірявши довжину і діаметр зразка після випробувань, можна підтвердити
незмінність форми і розмірів. Тому проводять крейдою пряму лінію на зразку (рис.
2.18), яка потім перетворюється у гвинтову. Випробування сталі на кручення більш
відповідальні, за інші випробування. Аналіз діаграми кручення підтверджує
наявність пружних властивостей матеріалу.
Випробування крихкого матеріалу. Чавун.
Чавунний зразок при крученні закручується на досить невеликий кут
закручування і руйнується відривом під дією нормальних напружень σ. А так як чавун – крихкий матеріал
і погано опирається розриву, то і на кручення він теж не має переваг у
використанні. За руйнівного навантаження Ммц визначається границя міцності σмц. Процес випробування
на кручення наочно відображається діаграмою кручення (рис.
2.22).
Випробування показують, що руйнування чавунних зразків відбувається
шляхом відриву по площині, нахиленої до осі зразка приблизно на кут α = 45° під дією нормальних напружень, які направлені перпендикулярно до
площини відриву (рис. 2.20, а).
Оснащення робочого місця:
v лабораторна установка – машина для випробування матеріалів на кручення
КМ-50;
v зразки
із сталі та чавуну;
v штангенциркуль;
v
методичні вказівки до виконання лабораторної роботи;
v калькулятор, олівець, лінійка;
v
журнал лабораторних робіт.
Порядок виконання випробувань
Робота проводиться на зразках двох видів: крихкий і пластичний. В
якості крихкого випробується чавун, а в якості пластичного – м’яка сталь. При випробуванні зразків проводиться
запис діаграми «крутильний момент –
кут закручування».
Лабораторна робота проводиться у такій
послідовності:
1. Розглянути ескізи зразків до випробування.
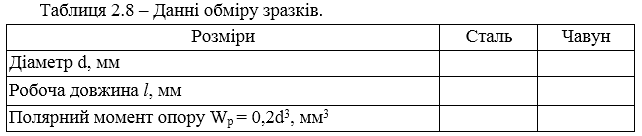
3. Перевірити готовність машини КМ-50 до роботи, шкалу силовимірювача
настроїти на максимальний крутильний момент 200Н·м.
4. На зразку по утворюючий поверхні нанести крейдою лінію, паралельну осі
зразка та закріпити зразок у затискачах випробувальної
машини.
5. Встановити необхідний масштаб запису крутильного моменту та кута
закручування.
6. Увімкнути машину, довести зразки до руйнування і записати діаграми на
діаграмному апараті.
7. За шкалою силовимірювача зняти величину крутильного моменту, що
відповідає руйнуванню зразків.
8. Визначити величину повного кута закручування (знімається з двох лімбів
машини): як суму кількості обертів малого лімбу і кута на великому
лімбі.
9. Перенести у журнал лабораторних
робіт діаграми кручення сталі та чавуну, приймаючи до уваги, що горизонтальну
вісь кута закручування необхідно повернути на кут tgα = 1/4.
10. Визначити основні механічні характеристики міцності та пластичності,
результати занести у таблиці 2. 9, 2.10.
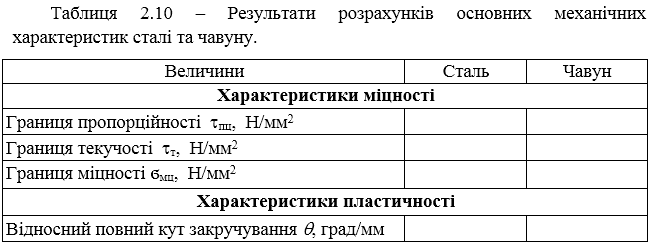
11.
Встановити і описати характер руйнування стального та чавунного
зразків.
12. Побудувати епюру розподілу дотичних напружень по висоті перерізу стального вала.
Використовуючи формулу (2.22) визначаємо дотичні напруження в центрі перерізу (в полюсі) та на поверхні вала. Зображуємо епюру (рис. 2.23).
13.
Відповісти на контрольні запитання.
14.
Захистити лабораторну роботу у викладача.
2.5. Лабораторна робота
ВИЗНАЧЕННЯ ТРЬОХ ПРУЖНИХ СТАЛИХ ВЕЛИЧИН Е, G, m
Мета роботи: ознайомлення з методикою вимірювання деформацій важільним тензометром та експериментальне визначення значень модуля пружності
І-го роду E, модуля пружності ІІ-го роду G і коефіцієнта Пуассона m для м’якої сталі.
Короткі теоретичні відомості
Багаторічна практика будування інженерних конструкцій, досвід їх
експлуатації і спостереження за поведінкою при різних типах зовнішніх впливів, в
тому числі, і руйнувальних показали, що лінійні і кутові переміщення конструкцій
в певних межах пропорційні діючим навантаженням. Вперше зазначена закономірність
була висловлена у 1678 р. Робертом Гуком у книзі «Про відновлювальну здатність
або про пружність», яка була першою
друкованою роботою щодо пружних властивостей матеріалів. Гук сформулював
свій закон наступним чином: «Яке
переміщення, така і сила».
Цей закон носить назву закону
Гука, є основним законом опору
матеріалів. Таке трактування встановлює співвідношення між переміщенням уA (кутовим або лінійним)
довільної точки А системи від зовнішнього навантаження F у вигляді:
.
У цій формулі Δ - деякий коефіцієнт, що залежить
від типу зовнішнього навантаження, місця його прикладання, положення точки А,
виду переміщення, геометричних особливостей тіла та фізико-механічних
властивостей матеріалу.
Геометричні зміни тіла є
проявом деформації її матеріалу, інтенсивність яких визначає міцність тіла в цілому.
Сучасне трактування закону
Гука таке: напруження прямо пропорційне відносній поздовжній деформації, з
урахуванням коефіцієнта пропорційності, яким є модуль пружності І-го роду
(модуль Юнга), яке відображається формулою (2.10). Зазначена залежність має
місце для пружних деформацій.
Модуль поздовжньої пружності є важливою механічною
характеристикою матеріалу, яка показує, як матеріал чинить опір деформаціям. Для
лінійно-пружних матеріалів він має постійне значення у межах зони
пружності.
З фізичної точки зору модуль поздовжньої пружності – це напруження, при
якому зразок збільшує свою довжину удвічі.
При осьовому розтягу або стиску елементи конструкції зазнають поздовжню
і поперечну деформації (рис. 2.24).
Поздовжня деформація це коли довжина бруса подовжується під час розтягу, або укорочується під час стиску. Поперечна деформація – коли поперечні розміри зменшуються під час розтягу, або збільшуються під час стиску.
Спостереження показують, що при розтягу в поздовжньому напрямку
подовження бруса збільшується (а це знак «+»), а поперечні розміри його
зменшуються (а це знак «–»).
Так само, як і модуль Юнга, коефіцієнт Пуассона є характеристикою
пружних властивостей матеріалу.
Для ізотропних матеріалів коефіцієнт Пуассона є однією з найбільш
важливих механічних характеристик. Його значення знаходиться у
межах:
0 ≤ μ ≤ 0,5.
Нижня межа, тобто μ = 0 свідчить про те, що це
матеріали, абсолютно не мають поперечного звуження при розтягу (і розширення при
стиску). Прикладом такого матеріалу є пробка. Верхня межа, тобто μ=0,5 свідчить про те, що це
пластичні матеріали, що змінюють при деформації тільки форму, але не об’єм (матеріал як би «перетікає» з однієї
форми в іншу, не розтягуючись по суті). Прикладами таких матеріалів можуть
служити парафін і деякі каучуки. Отримані з багатьох експериментів значення
коефіцієнта Пуассона однакові як при розтягу, так і при стиску.
Середньостатистичні значення μ для широкого кола різних металів
при інженерних розрахунках зазвичай приймають рівними
0,30.
Для найбільш поширених матеріалів значення коефіцієнта Пуассона зведені до таблиці 2.11.
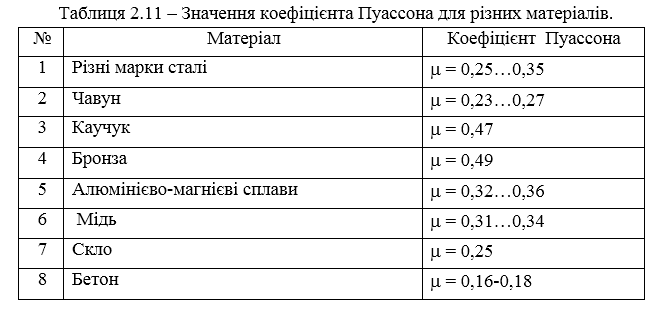
Модуль пружності другого роду характеризує пружні властивості ізотропних твердих тіл в
умовах деформації зсуву. Тому частіше його ще називають модулем зсуву.
Довільну деформацію ізотропного твердого тіла можна розбити на дві важливі складові – деформацію розтягу або стиску, яка пов’язана зі зміною лінійних розмірів тіла, та деформацію зсуву, при якій змінюється форма тіла.
Із розгляду деформації чистого зсуву шляхом перетворень з урахуванням узагальненого закону Гука для плоского напруженого стану модуль пружності ІІ-го роду G визначається за формулою:
Прийнято вважати, що формула (2.27) пов’язує між собою три пружні сталі
величини: модуль пружності І-го роду Е, модуль пружності ІІ-го роду G та коефіцієнт Пуассона µ.
Модуль пружності ІІ-го роду при зсуві, так само як і модуль Юнга при
розтягу-стиску, є коефіцієнтом пропорційності, який пов’язує дотичні напруженням
τ
та кутову деформацію γ:

Вираз (2.28) має назву закона Гука при зсуві і встановлює прямо-пропорційний зв’язок між напруженням τ та деформацією γ..
Для найбільш розповсюджених матеріалів модуль зсуву G має
наступні значення (табл. 2.12):
Дослідження пружних сталих величин проводять на зразку прямокутного
перерізу (рис. 2.1, г), прикладаючи до нього осьове розтягуюче навантаження.
Форма зразка регламентується ГОСТом.
Лабораторні дослідження проводяться з використанням універсальної
випробувальної машини УИМ-50, встановлюючи зразок в затискачі машини, як
показано на рисунку 2.25, а. У трьох напрямках до зразка кріпляться тензометри
(рис. 2.25, б). Два з них (лівий і правий) призначені для вимірювання поздовжніх
деформацій, а один (середній) – для вимірювання поперечної
деформації.
Оскільки випробування повинні відбуватись у межах пружних
деформацій, то спочатку треба визначити максимальне навантаження, при якому
напруження не перевищують границі пропорційності:
.
А
потім, проводжуючи дослідження, прикласти статичне навантаження до границі
пропорційності.
Оснащення робочого місця:
v лабораторна установка – універсальна випробувальна машина УИМ
-50;
v стальний зразок прямокутного перерізу, встановлений у затискачах
машини;
v важільно-стрілочний механічний тензометр Гугенбергера – 3
шт;
v методичні вказівки до виконання лабораторної
роботи;
v калькулятор, олівець, лінійка;
v
журнал лабораторних робіт.
Порядок виконання випробувань
Експериментальне визначення модуля Юнга, модуля зсуву і
коефіцієнта Пуассона проводиться на сталевому зразку у вигляді довгої пластини,
що піддається розтягуванню.
Лабораторна робота проводиться у такій
послідовності:
1. Виміряти розміри зразка та визначити площу поперечного
перерізу.
2. Встановити зразок в затискачах випробувальної
машини.
3. Підібрати три
тензометри з однаковою базою та закріпити їх на зразку згідно схеми (рис. 2.26). База тензометрів повинна складати
20мм.
4. Визначити початкове та максимальне навантаження, зробити експеримент при шістьох рівнях навантаження, при цьому ΔF = 20кН.
5. При кожному рівні навантаження зняти показання з тензометрів та
занести до журналу спостережень (табл. 2.12), підрахувати абсолютну різницю
показань.
6. Провести обробку результатів вимірювань
Визначити середні значення прирощень показників поздовжньої деформації (тензометри А) та поперечної деформації (тензометр В):
7. Визначити значення поздовжньої та поперечної деформації за формулами:
11. Порівняти отримані результати випробувань з довідковими даними
(табл. 2.13).
12. Відповісти на контрольні запитання.
13. Захистити
лабораторну роботу у викладача.
2.6. Лабораторна робота
ВИЗНАЧЕННЯ УДАРНОЇ В’ЯЗКОСТІ СТАЛІ ПРИ
УДАРНОМУ ЗГИНІ ТА РОЗТЯГУ
Мета роботи: дослідження поведінки сталевих зразків під час ударного згину і розтягу та визначення питомої ударної
в’язкості.
Короткі теоретичні відомості
Рішення інженерних задач базується на наближеній теорії пружного удару,
у якій приймаються такі основні припущення:
1. Кінетична енергія тіла, що вдаряється, цілком переходить у потенційну
енергію деформацій, при цьому зневажають енергією, яка йде на деформацію тіла,
що вдаряється.
2. Закон розподілу напружень і деформацій по об’єму тіла залишається
таким же, як і при статичній дії сил, при цьому не враховується зміна розподілу
напружень і деформацій у тому місці, де відбувається співудар тіл, а також за
рахунок коливань високої частоти, що супроводжують явище удару у всьому обсязі
тіла.
Припустимо, що дуже жорстке тіло А
вагою Q, деформацією якого можна
зневажати, падаючи з деякої висоти h, ударяє по іншому тілу В, яке опирається на пружну систему С. В окремому випадку це може бути
падіння вантажу на кінець призматичного стержня, інший кінець якого закріплений
(поздовжній удар), падіння вантажу на балку, що лежить на опорах (згинаючий
удар).
Матеріал у порівнянні зі статичним навантаженням інакше реагує на удар.
Одержані при статичних випробуваннях, тобто під дією дуже повільно
наростаючого навантаження, механічні характеристики не можуть оцінити здатність
матеріалу протистояти ударному навантаженню. Випробування на ударну в’язкість
відносяться до динамічних видів випробувань, які застосовують, щоб оцінити
властивість матеріалів витримувати ударні навантаження. Ці випробування особливо
важливі для високоміцних сплавів, які можуть мати задовільні характеристики
пластичності при звичайних випробуваннях, але крихко руйнуються у реальних
конструкціях при наявності концентраторів. Швидкість деформування і деформація
при динамічних випробуваннях на декілька порядків більші, ніж при
статичних. При великих швидкостях збільшується небезпека крихкого руйнування. Ця
небезпека особливо зростає при наявності в деталі різного роду надрізів (отвори,
виточки, галтелі, канавки і т. п).
Зазначені
обставини призводять до необхідності введення деякої характеристики, що дає
оцінку поведінки матеріалу при динамічних навантаженнях і виявляє небезпеку
крихкого руйнування. Для цього призначені
спеціальні випробування на ударну в’язкість – ударна проба
матеріалу.
Ударна
в’язкість – це
складна комплексна характеристика, яка залежить від декількох більш простих
механічних властивостей.
Випробування на удар проводять на спеціальних маятникових копрах із застосуванням стандартних зразків. Щоб можна було порівнювати отримані результати, ГОСТ 9454-78 стандартизує методи визначення ударної в’язкості, форму й розміри зразків, надрізів (рис. 2.27), а також умови їх механічної обробки, якість обробки поверхні, оскільки всі ці фактори впливають на величину ударної в’язкості.
Необхідність стандартизації викликана тим, що неоднорідність напруженого стану в зоні надрізу і складність явищ, які протікають при ударному руйнуванні, не допускають застосування закону подібності (як, наприклад, в разі розтягу гладких зразків). Це означає, що для геометрично подібних, але різних за розмірами зразків величина ударної в'язкості не буде однаковою, вона залежить від температури зразка при випробуваннях.
Ударний згин
зразка
Найбільш поширеним
видом ударних випробувань є випробування на ударний згин зразка з надрізом,
загальний вигляд якого зображено на рисунку 2.27, а. На рисунку 2.28 зображено ескіз зразка
з надрізом. Надріз роблять для того, щоб створити додаткову умову, що полегшує
крихке руйнування зразка. Поблизу надрізу виникає об’ємний напружений стан
(тривісний розтяг), що ускладнює розвиток пластичної деформації і сприяє
крихкому руйнуванню.
Наявність різкого переходу в розмірах поперечного перерізу виробу, а також перші сліди тріщин сприяють виникненню крихкості та викликають передчасне руйнування матеріалу. Тому випробовувані зразки надрізають з одного боку, щоб викликати в них різку неоднорідність напружень при ударі й ускладнити пластичну деформацію, що полегшує оцінку схильності металу до переходу в крихке становище.
Ударна в’язкість при згині
визначається як відношення роботи A, необхідної для руйнування ударом
спеціального зразка, до площі поперечного перерізу в місці надрізу:
де – питома ударна в’язкість,
Дж/м2;
А – робота, витрачена на руйнування (злом) зразка при ударі, Дж;
S– площа перерізу
зразка в місці надрізу (рис. 2.28), м2.
Чим більш пластичний матеріал, тим більше величина роботи, що
витрачається на його руйнування. Тобто пластичний матеріал краще чинить опір
ударним навантаженням.
Величина ударної в’язкості залежить від температури зразків при випробуваннях. Для порівняльної оцінки якості матеріалу проводять випробування при кімнатній температурі. Ударна в’язкість сильно залежить також від наявності різного роду дефектів в структурі металу (тріщини, порожнечі, неметалеві включення та ін.). Тому випробування на ударну в’язкість відносяться також до числа поширених технологічних проб, які виявляють якість матеріалу. При ударному згині пластичний матеріал змінює свої властивості і руйнування набуває крихкого характеру (рис. 2.29, б).
Поява крихкого зламу пояснюється тим, що діаграма розтягу волокон, що
прилеглі до надрізу, і особливо границя текучості сильно підвищені, як під
впливом швидкості, так і під впливом надрізу, що створює різкий градієнт
напружень і тим ускладнює деформацію. А істинний опір розриву не залежить від
цих чинників і, при досить інтенсивній дії останніх, може виявитися нижче опору
пластичної деформації (границі текучості). Завдяки цьому, на появу крихкості
впливають:
а) температура зразка, при зниженні якої підвищується границі текучості,
збільшуючи внутрішнє тертя, що полегшує появу крихкості;
б) швидкість удару, збільшення якої також підвищує границю текучості;
в) форма зразка, так як широкі зразки з ускладненою поперечною
деформацією легше призводять до крихкого зламу, ніж вузькі.
Крихкий злам при кімнатній температурі проявляється у таких матеріалів,
що пройшли неналежну термічну і механічну обробку, наприклад, крупнокристалічне
залізо (рекристалізація після появи критичного наклепу), зістарене залізо (що
отримало деформацію при 200-300°С), хромонікелева сталь, відпущена з малою
швидкістю охолодження (крихкість відпустки), інші види випробування, в тому
числі ударний розрив. Випробування на удар без надрізу застосовується тільки під
час випробувань колій.
Наявність різкого переходу в розмірах поперечного перерізу виробу, а
також перші сліди тріщин сприяють виникненню крихкості та викликають передчасне
руйнування матеріалу. Тому випробовувані зразки надрізають з одного боку, щоб
викликати в них різку неоднорідність напружень при ударі й ускладнити пластичну
деформацію, що полегшує оцінку схильності металу до переходу в крихке становище.
Біля дна надрізу при ударі, внаслідок різкої зміни площі поперечного
перерізу разом з напруженнями, спрямованими уздовж осі зразка, з’являються
напруження, перпендикулярні до осі, тобто виникає об'ємний напружений стан із
позитивними головними напруженнями. Ці напруження ускладнюють пластичну
деформацію в матеріалі зразка. Ще більш суттєве те, що надріз зосереджує всю
деформацію, поглинаючи енергію удару, в порівняно невеликому об’ємі
матеріалу.
Ударні випробування зразків на ударний згин проводять на маятниковому
копрі МК-30 з граничною енергією копра 300 Дж. Швидкість ножа копра змінюється
від 4 до 7 м/с, що відповідає підняттю ножа маятника на висоту від 0,8 до 2,6
м.
Роботу, що витрачається на руйнування зразка, визначають, як різницю запасів енергії маятника до і після удару:
А = mg·(H
– h),
де Н – висота підняття центру ваги маятника до удару,
м;
h – висота підняття центру ваги маятника після удару,
м.
Ударний розтяг зразка
Для випробувань на ударний розтяг використовують зразок циліндричної форми (рис. 2.31), на кінцях якого нарізана різьба, довжиною ℓ2.
Один кінець зразка вкручують в спеціальне пристосування в молоті маятника, а на другий накручують «тарілку» (рис. 2.32).
Розтягуюче навантаження миттєво подається на зразок в момент удару
фіксуючого бруска по ковадлах. Цей тип кріплення зразка дає постійний розподіл
енергії удару в розрахунку на площу зразка. Після випробування на ударний розрив
отримуємо зразок з такими ж наслідками, як і при випробуванні на статичний
розтяг. За короткий період часу зразок стає довшим, з’являється слабке місце –
«шийка» і відбувається відрив (рис.2.33).
Характер руйнування зразка –
відривання зі зсувом.
При ударному розриві деформації та напруження залежать від довжини
стержня ℓ0 і модуля поздовжньої
пружності Е. Таким чином, для зниження
напружень збільшують довжину зразка. Отже, при поздовжньому ударі величина
напружень залежить від об’єму. Таким чином питома ударна в’язкість визначається як відношення роботи, витраченої на руйнування зразка, до його об’єму:
де – питома ударна в’язкість,
Дж/м3;
А – робота, витрачена на руйнування
(розтяг) зразка при ударі, Дж;
Роботу руйнування визначають на спеціальному ударному копрі Шарпи,
визначаючи кут підйому маятника після удару. По спеціальним таблицям (Додаток 4) цей кут переводять в роботу
руйнування.
У результаті випробувань завжди виявляється, що динамічний тимчасовий
опір вище статичного (перевищення до 100%), границя текучості також підвищена, і
до того ж більша ніж тимчасовий опір на 20-60%. Подовження або дорівнює або
більше статичного; звуження шийки майже таке ж саме. Характерна ударна крихкість
проявляється при цьому випробуванні у дуже небагатьох металів (наприклад у сталі
з вмістом фосфору > 0,10%).
Вимірювання сил при ударі представляє великі труднощі і у лабораторну
практику ще не увійшло. Одним з недоліків традиційного методу випробування на удар є те, що в
результаті визначається лише сумарна енергія руйнування. Іноді застосовують
інструментальні методи контролю випробування, суть яких полягає в безперервному
вимірюванні навантаження в процесі руйнування. Це дає можливість для оцінки крім
енергії руйнування ще й максимального зусилля при руйнуванні, що дозволяє
оцінити перехід від крихкого до пластичного механізму руйнування при зниженні
температури.
Оснащення робочого місця
v лабораторні установки – маятниковий копер МК-30А та копер
Шарпі;
v зразки на ударний розтяг та згин;
v методичні вказівки до виконання лабораторної
роботи;
v калькулятор, олівець, лінійка;
v
журнал лабораторних робіт.
Проведення випробувань
Робота складається
з двох етапів: на першому етапі проводимо випробування на ударний згин, на
другому етапі – випробування на ударний розтяг.
Лабораторна робота проводиться у такій
послідовності:
1.
Перед
випробуваннями слід обміряти розміри зразків: на ударний згин – у місці надрізу,
на ударний розтяг – робочу довжину і діаметр.
2.
Для випробувань
на ударний згин: встановити відстань між опорами. Якщо поперечний переріз зразка
становить 10х10мм2, то відстань між опорами 40 мм.
3.
Злегка
відхиливши маятник в сторону його підйому, покласти зразок на опори так, щоб
удар падаючого маятника припадав з боку, протилежного надрізу, відносно опор з похибкою не більше ±0,5
мм, а надріз знаходився в одній площині з вістрям ножа маятника (рис. 2.30,
б).
4.
Підняти
маятник на висоту, відповідну енергії удару, що задається і закріпити защіпку
стопором. Не рекомендується встановлювати надмірно велику енергію удару в
порівнянні з необхідною для руйнування зразка, так як це знижує точність
результату випробування.
5.
Звільнити
запобіжник, маятник вільно падає, руйнуючи зразок. При цьому покажчик шкали
покаже величину роботи, витраченої на руйнування зразка. Після
руйнування зразка зупинити гойдання маятника гальмом.
6. Знайти енергію, витрачену на руйнування зразка Aн = A0 – A1.
7. Визначити ударну в’язкість матеріалу зразка aн. Результати
розрахунків занести у таблицю 2.14.
8.
Для випробувань
на ударний розтяг: накрутити на один кінець зразка спеціальний пристрій
«тарілку», а другий вкрутити в молот маятника.
9.
Підняти
маятник на висоту, що відповідає нульовій відмітці на шкалі силовимірювача і
закріпити запобіжником.
10. Звільнити запобіжник. Розтягуюче навантаження миттєво подається на зразок у момент удару фіксуючої «тарілки» бруска по ковадлах Зупинити маятник при зворотному ході за допомогою стрічкового гальма.
11. Визначити за шкалою копра кут зльоту маятника після удару, та за допомогою спеціальних таблиць перевести його в роботу руйнування.
12. Визначити об’єм робочої частини зразка та розрахувати ударну в’язкість матеріалу aн. Результати випробувань занести у таблицю 2.15
13.
Під час
проведення випробувань висувають наступні вимоги: при вирізанні заготовок метал
зразків не повинен піддаватися наклепу та нагріву, які змінюють властивості
металу; якщо в результаті випробування зразок не зруйнувався повністю, то
показник якості матеріалу вважається не встановленим.
14.
Відповісти на
контрольні запитання.
15.
Захистити
лабораторну роботу у викладача.
Тестові запитання для самоконтролю
1. Що таке динамічне навантаження?
короткочасний силовий вплив;
навантаження, що відповідає границі
пропорційності;
навантаження, що відповідає границі міцності.
2. Величина, що оцінює вплив частоти вимушених коливань
називається:
коефіцієнтом динамічності;
коефіцієнтом пружності;
коефіцієнтом запасу міцності.
3. Навантаження, при якому швидкість деформування взаємодіючих тіл,
змінюється за короткий період часу називається:
ударним;
статичним;
крутильним.
4. Відношення роботи руйнування стандартного зразка до площі його
поперечного перерізу в місці надрізу називається:
питомою ударною в’язкістю;
коефіцієнтом запасу міцності;
границею міцності.
5. За допомогою якого пристрою проводять випробування на
удар?
маятниковий копер;
крутильна машина;
універсальна розривна машина.
6. Зразок якого перерізу використовують на ударний
згин?
прямокутного;
круглого;
двотаврового.
7. Зразок якого перерізу використовують на ударний
розтяг?
круглого;
прямокутного;
двотаврового.
8. Що характеризує здатність матеріалу протистояти крихкому
руйнуванню?
ударна в’язкість;
границя міцності;
відносне залишкове видовження.
9. Для чого роблять надріз на зразку при випробуваннях на ударний
згин?
для того, щоб створити концентратор напружень;
для того, щоб зразок не перевернувся;
для того, щоб зразок розтягнувся.
10. Для чого проводять випробування на ударну в’язкість?
щоб оцінити властивість матеріалів витримувати ударні
навантаження;
щоб оцінити опір розриву;
щоб оцінити властивість матеріалу витримувати зовнішні
навантаження.
11. Яку геометричну характеристику використовують при ударному розтягу?
об’єм зразка;
момент опору перерізу зразка;
момент інерції перерізу зразка.
12. Яку геометричну характеристику використовують при ударному згині?
площу перерізу зразка;
момент інерції перерізу зразка;
момент опору перерізу зразка.
13. Як визначають роботу руйнування при ударних випробуваннях на
маятниковому копрі?
як різницю запасів енергії маятника до і після
удару;
як суму кінетичної та потенційної енергії;
як різницю зовнішніх сил.
14. Яким символом позначається робота руйнування?
А;
F;
σт.
15. Одиниці вимірювання роботи руйнування при ударі?
Дж;
МПа;
Н.
16. З яких одиниць складається Джоуль?
Н·м;
Н/м2;
кН.
17. Який характер руйнування
зразка з пластичного матеріалу під час випробувань на ударний
згин?
крихкий;
пластичний;
стійкий.
18. Одиниці вимірювання питомої ударної
в’язкості?
19. Яким символом позначається питома ударна в’язкість?
20. Який діаметр зразка, що використовують при випробуваннях на ударний
розтяг?
5мм;
10мм;
15мм.
.